Not wanting to do the typical waffle structure or a typical stacked or layered serial study. I was looking through P. Scott's favorites of Flickr and came across something that sparked my interest
http://www.flickr.com/photos/26440532@N07/sets/72157621046981164/and ran with it and did a little more research.
While researching I found that a reputable digital fabricator/ architect Mark Fornes "Thevermany" is doing a much more complex but similar project
http://www.theverymany.net/labels/weaving.html.
Here is a little about my process I took five curves that I wanted to be the dowels suppporting the vertical planes
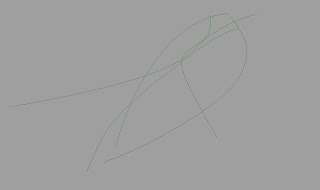
Once I had these curves I lofted them as straight sections rather than the normal curvilinear style and selected a closed loft resulting in this shape.
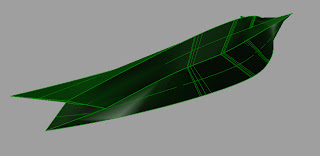
After I had this form I needed to make a place for the dowels to run through, so I used the pipe command on the same curves that I lofted and made them a 1/2" diameter and booleaned the loft and the pipe together.
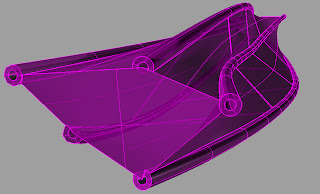
Then still using the same curves I once again used the pipe tool, but this time I made the pipe a 1/4" diameter and used the boolean-difference tool to make the 1/4" pipe hollow. Then I contoured the form ever 1 1/2" and layed it out for laser cutting.
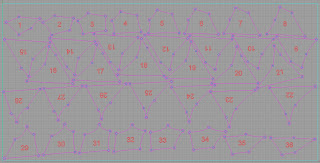
This is also the project that I will be rendering in a architectural setting and here's the camera angle I'm rendering.
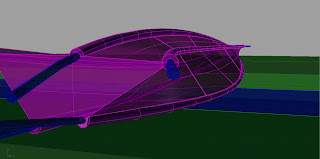
Building this was quite the treat. I took 5 1/4" dowels and 360 1/4" e-clips. The e-clips go on both sides of the vertical planes on all 5 dowels. I made a jig with spacers to get the correct 1 1/2" spacing between the contours.
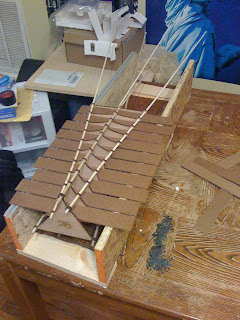
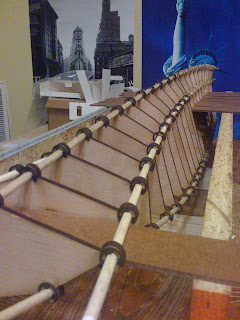
So here is the final product in some sexy lighting
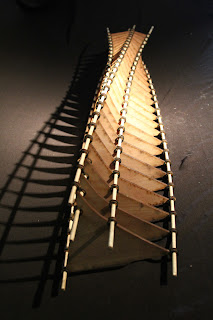